Don Warsing: Focused on Improving Operational Outcomes
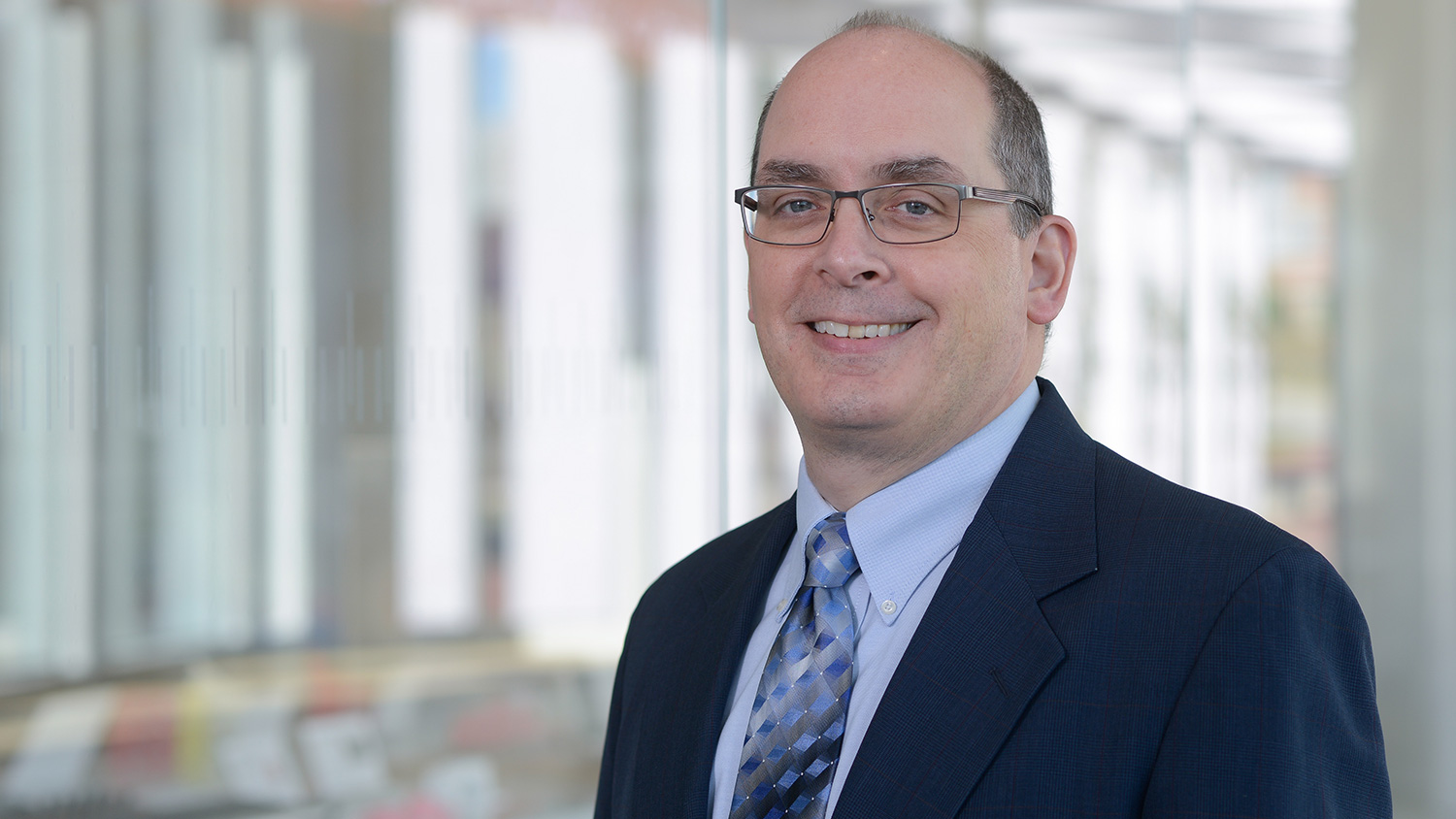
“I definitely consider myself an engineer that crossed over into management,” says Don Warsing, Ph.D., associate professor of operations and supply chain management in the NC State Poole College of Management.
He actually bridges the two disciplines, as Warsing also has associate faculty status with the Edward P. Fitts Industrial and Systems Engineering (ISE) Department in NC State’s College of Engineering and is one of the thought leaders in Poole College’s Supply Chain Resource Cooperative.
The engineering-business intersection “is pretty common among industrial engineers, since that discipline really strives to connect the technical and management sides of any business,” he said.
Warsing began his career as an industrial engineer at IBM, supporting manufacturing departments through work methods studies, capacity analysis, and process flow improvements. “I eventually worked my way through materials management, quality engineering, and up to managing a manufacturing department,” he said.
“I found that I really liked working to solve problems where you could see the improvements being implemented on a daily basis. That search for improved operational outcomes is what I still get to work on every day, just in a much more abstract and theoretical sense in my current work,” he said.
While at IBM, Warsing began working on his Master of Science in Management at NC State, the precursor to what is now Poole College’s Jenkins MBA degree.
“The MSM program required students to write a committee-advised final project paper. My project involved a large process improvement initiative for the service parts fulfillment process I supported as an engineer and that I eventually managed in my last work assignment at IBM,” he said.
“I really enjoyed working on that project and applying the tools I was learning about in the MSM program. I ultimately reviewed the final report and recommendations with my manager, who was responsible for the bulk of our site’s aftermarket support and product recovery operations,” Warsing said.
His manager was “very supportive of implementing much of what I was recommending, but I didn’t stick around to see it implemented. At that point, the academic bug had fully set in for me, and I was on my way to a major life transition from the business world to the academic world,” Warsing said. He went on to earn his doctorate in operations management from the University of North Carolina at Chapel Hill, in 2000.
Prior to joining Poole College’s faculty in 2003, Warsing served on the faculty of the Smeal College of Business at Pennsylvania State University.
Warsing shared key insights gained through his industry experience and academic research in an email interview with Poole College communications.
Managing Uncertainty: Measuring and Strategically Buffering
An overriding concern in operations management is understanding how to manage uncertainty, which presents itself in almost every aspect of supply and demand related to the business. There are two key aspects to managing uncertainty: measuring it and strategically buffering to mitigate its effects.
The strategic aspect of buffering for the firm involves choosing the nature of the buffers, he said. “A widely accepted framework for this is that buffers are based on some combination of inventory, capacity, and time. The key for the business is to understand how this choice of buffers best fits into its broader strategy in terms of marketing – who its customers are and what they want – and finance – how the business will obtain and deploy financial capital.
“So, the operations of the business serve as the connecting point that utilizes the firm’s capital to transform inputs into outputs to serve the firm’s customers,” he said.
“But, for me, it’s the grittier details of the analysis that really resonate, and I try to impress upon my students that the ‘roll up your sleeves and crunch the numbers’ aspect of operations management is where they can really make a difference. Ultimately, management needs to have a good grasp on the underlying analysis in order to make effective decisions at both tactical and strategic levels,” Warsing said.
A Harvard Business School interview that he read recently “pointed out that, while many managers like to think of themselves as ‘number crunchers,’ they are more likely to be ‘idea crunchers’ that sidestep the grunt work of digging into the numbers. The current trend to emphasize analytics is really changing that, though, and no doubt for the better, as far as I’m concerned,” he said.
Bridging the Industry-Academy Gap
Frustration over management’s focus “on putting out day-to-day fires but never stepping back to take a broader look at why the day-to-day fires kept springing up” drew Warsing to the academic world, where “the hope is that the long-time-scale approach we take in academics to diving deeply into really challenging problems can ultimately connect back to keeping the fires from starting in the first place,” he said.
“The SCRC provides a tremendous opportunity to make those short-term/long-term connections. A great example of this was a recent meeting that some of my Poole and ISE colleagues had with a technology company that had invited us in to talk about a particular challenge they are facing and their hope of building a long-term solution to it by drawing on how academics have approached the problem,” he said.
“The meeting resulted in an agreement to start with an SCRC student project focused on data gathering and analysis, using that as a stepping stone to identifying the bigger-picture aspects of the problem that could frame a broader, longer-term academic analysis. It was a very encouraging meeting and what I hope is the start of a fruitful engagement,” he said.
Warsing said he enjoys working with student teams on their SCRC industry projects. “In a typical semester, about two teams will approach me to seek advice, and that typically results in two or three meetings with the team throughout the semester. Meetings like that have so many beneficial aspects. The students not only get to see that class concepts are indeed relevant to real problem solving, but also that working through the messy details of reality is a lot harder than solving the back-of-the-book problem that gives them all the problem parameter values,” he said.
“And, I get to see better how to connect what I’m doing in class and research with the issues that businesses are wrestling with,” he said.
“I also love to receive messages from students telling me about how their job connects to what they learned in class. I got one of those just a couple of weeks ago, with the subject line “Using 470!” and telling me about computing the capacity of a newly installed machine in the production process to demonstrate its benefit to the business. Those kinds of messages warm my number-crunching, ops-guy heart!”
Warsing’s research continues to focus on the development of tools and policies for effectively managing inventory, logistics, and business operations, and studying the way in which various management practices contribute to improved performance outcomes. His work has been published in Production and Operations Management, the Journal of Operations Management, Decision Sciences, and the European Journal of Operational Research, among others. He is also the co-author of a graduate-level textbook, Supply Chain Engineering: Models and Applications (CRC Press, 2012).