Robots and Remote-Control Machines? Students Discuss Global Sourcing, Supply Chain at Caterpillar Plant

By Jess Clarke
Poole College of Management economics student Jack Robinson spends a lot of time monitoring timber and feed-grain markets for research topics — online. That means he doesn’t have much contact with the people directly involved in the issues he studies.
A recent visit to the Caterpillar plant in Clayton, North Carolina, gave him an opportunity to talk with managers about global sourcing, supply chain and other aspects of business, and to watch the assembly line.
“To go out and talk to people with boots on the ground and get their perspective was invaluable,” says Robinson, who will earn a master’s degree in economics at NC State in May and expects to finish Poole’s doctoral program in 2024.
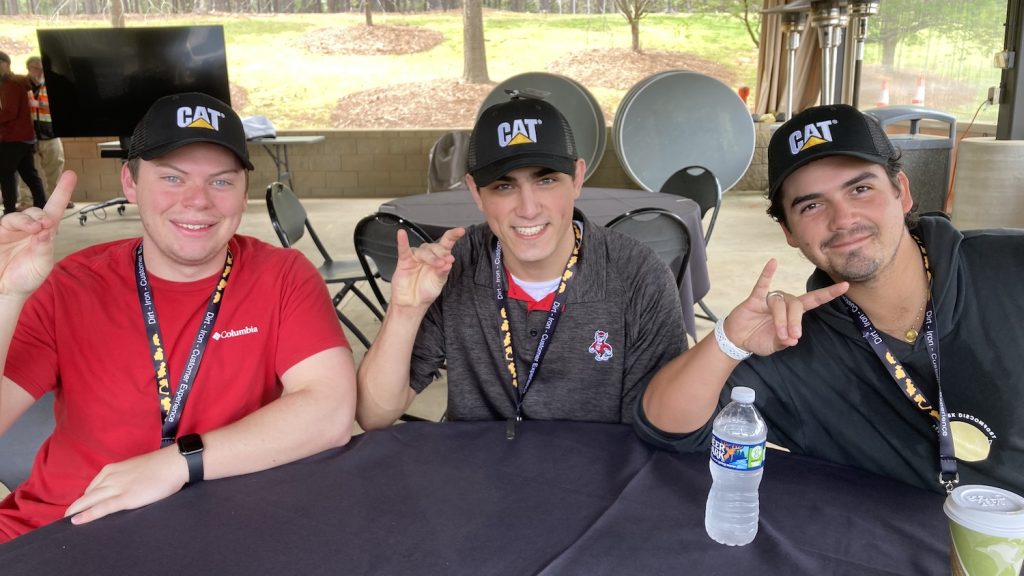
He was among about 35 students, faculty and staff who visited the plant on a trip organized by Luca David Opromolla, Owens Distinguished Professor of international economics at Poole.
Students Gain Valuable Insights from Caterpillar Managers
No matter which major Poole students are pursuing, global sourcing strategies and supply chain have an impact on their field.
Whether a company buys inventory from independent suppliers or makes parts in another country at its own plant, sourcing and supply “are especially important now. The pandemic is causing lots of delays in delivery of goods and inefficiencies in production,” Opromolla says.
At Caterpillar, Poole students talked with Mehdi Daragheh, global engineering and sourcing manager; Dave Emonson, general manager for building construction products; Alfredo Garcia, supply chain manager; and Cody Smith, business support manager in the finance division.
The managers discussed a range of issues, including Caterpillar’s decision to source products in other countries, who the company’s suppliers are, and where it chose to operate factories.
It was incredibly interesting to hear them talk about the difficulties they’d been facing and their overall strategy of sourcing and supply chain.
“It was incredibly interesting to hear them talk about the difficulties they’d been facing and their overall strategy of sourcing and supply chain” while explaining how they’ve adapted to the pandemic, Robinson says.
Watching AI, Assembly Line in Action
The Clayton plant, with about 600 manufacturing employees, assembles small wheel loaders used in housing and highway construction, agriculture, recycling and other industries to lift materials.
The loader engines are built at a Caterpillar plant in the United Kingdom and shipped to the U.S.A Caterpillar facility in Mexico that supplies the Clayton plant’s fabrications. “Sourcing teams work to find the best suppliers for every part of the loaders,” says Olivia Lampe, customer experience coordinator in Clayton.
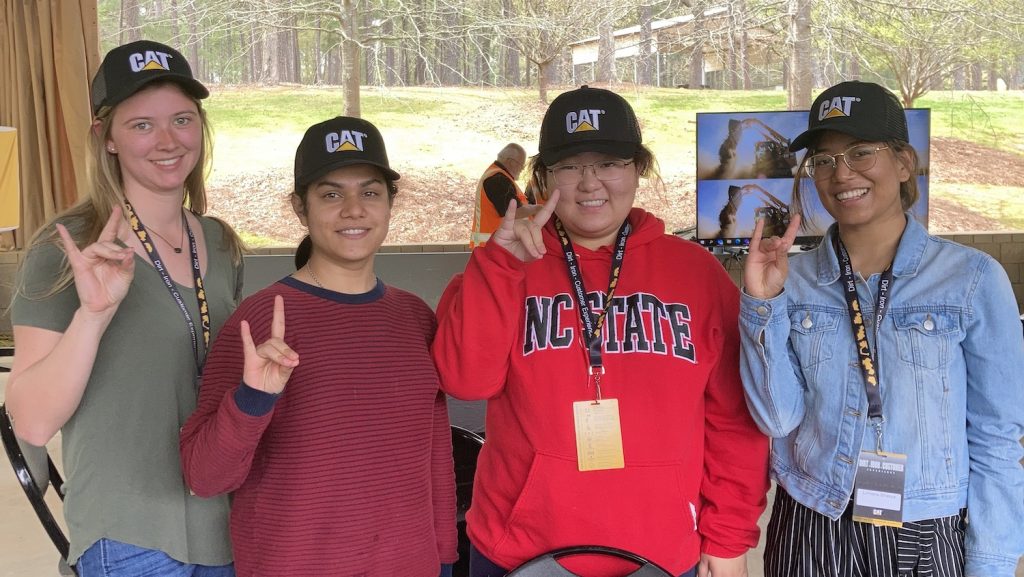
In addition to sourcing strategies, Poole students learned about new technologies, such as artificial intelligence, used in Caterpillar’s business processes. They were impressed by robots and remote-control machines at the Clayton plant.
Assembly line employees, for example, order parts for their stations with iPads, and robots deliver the inventory directly to them. “Seeing the integration of automation into their production process…was very cool,” Robinson says. “The workers can be focused on more value-added activities.”
Worker Accountability Increases Efficiency
For business administration student Elisa Piazzoli ’23, the plant visit reinforced concepts in her supply chain courses.
At Caterpillar, she learned that employees are cross-trained to work at assembly-line stations before and after their own station, so they can fill in if needed. A system with red and green lights signals to workers if a station is on time or not.
“They stress the accountability of each worker being in charge of his workstation…That’s how they try to make the process more efficient,” Piazzoli says. “It was fascinating because that’s what we’re studying in class.”
It was fascinating because that’s what we’re studying in class.
Although the Clayton plant uses innovations that promote efficiencies in production, robots and other automation aren’t an obstacle to workers’ input and professional development.
“The human component is very important. This connects with the overall business culture we saw at Caterpillar,” Opromolla says. “Everybody can be involved in all sorts of decisions. They try to include everyone at many different steps.”
Former Caterpillar chairman and CEO James W. “Jim” Owens, a Poole alumnus, former NC State Board of Trustees chairman, and three-time NC State graduate, has created several endowed Poole faculty positions, including Opromolla’s.
Plant Visit Reinforces Classroom Learning
The relationship between Caterpillar and Poole College is win-win. The Clayton plant hires Poole graduates and interns.
Visits to the plant by Poole students and faculty are enlightening for Caterpillar managers, too. “With college students so eager to learn…they’re asking bigger-picture questions that put things into perspective for us, so that’s a cool opportunity,” says Lampe, a 2018 Poole graduate.
Since visiting Caterpillar, Piazzoli no longer has to imagine how items actually move from station to station on an assembly line when looking at an Excel spreadsheet — she’s seen it in person.
And she may have seen her future. “The trip definitely helped me understand that supply chain is what I really like,” she says. Piazzoli, in the International Business Dual Degree Program, also is pursuing a degree at a university in her native Italy.
“I’m realizing more and more how important supply chain is,” she says. The Caterpillar experience “helped me see how a production plant works and what a career in supply chain might be.”
- Categories: