COVID-19 and Triple-A Supply Chains – Lessons Learned
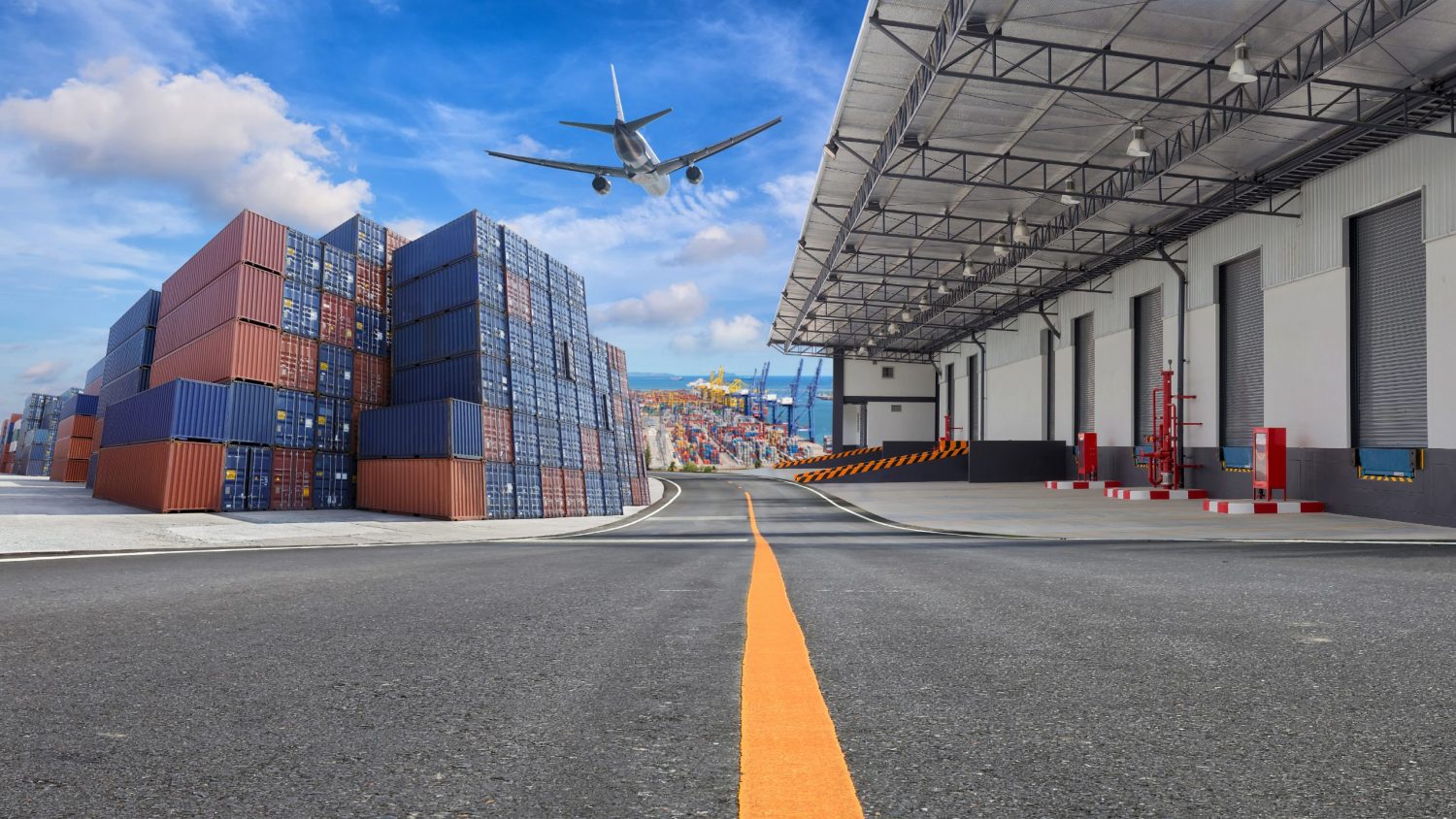
By Caroline Barnhill

As COVID-19 forces companies to examine their existing operations, supply chains are under the microscope. Tim Kraft, assistant professor of operations and supply chain management at Poole College of Management, shares some insight on supply chain lessons learned.
Triple-A Supply Chains: Agility. Adaptability. Alignment.
The recent crisis involving the COVID-19 pandemic has brought to mind a concept that I teach in my Operations Strategy course called Triple-A Supply Chains. The idea is about 15 years old, but it has never felt more appropriate.
Proposed in the early 2000s by Dr. Hau Lee, Stanford University’s Thoma Professor of Operations, Information & Technology, his observation was that having a fast and cost-effective supply chain did not necessarily lead to a competitive advantage. In fact, many companies with fast and cost-effective supply chains often saw their competitive position deteriorate over time.
Instead, the supply chains that provided companies with a competitive advantage displayed three traits: agility, adaptability and alignment.
Lee’s observations were primarily from a market performance perspective, however, the insights ring true in the present-day environment of COVID-19 (not to mention Tariff wars, global warming, and the numerous other disruptions occurring in supply chains).
Agility refers to the ability to react to sudden changes in demand. It is a lesson supply chain managers across all industries are currently experiencing as they work tirelessly to meet unforeseen spikes in demand and deal with shortages in supply created by COVID-19. Take, for example, the grocery industry. While consumers may worry that the empty shelves in their grocery stores suggest the food supply is at risk, I’m confident in our grocery supply chains. They are some of the most stable and resilient supply chains in the industry. It’s important to recognize that the grocery industry faced an unprecedented spike in demand the last month from (1) consumers over-purchasing out of fear and (2) the large shift from dining out to at-home eating. The fact that you are able to go to the store and find 75 percent of your grocery list is a testament to the agility of grocery supply chains. Demonstrating the ability to seamlessly source products from multiple locations, perform necessary and rapid trans shipments between stores, ration products by regions and locations, and expedite shipments are all signs of an agile supply chain.
Adaptability reflects the ability of a supply chain to adjust to a changing marketplace. Consider, once again, the grocery industry. Over the past decade, grocers have battled to see who would prevail as the market leader for online grocery. Ideas have been funded and failed for figuring out how to complete the mythical last-mile delivery to homes. For example, grocers have tried a range of methods including store pickups, thirty-party and peer-to-peer delivery, and third-party centralized delivery sites. While the potential revenues from online grocery have always been enticing, very few grocers have been able to figure out a customer-friendly model that also makes a decent margin. With the rise of the COVID-19 pandemic, grocers no longer have the benefit of time to test their different delivery models. COVID-19 has dramatically accelerated the movement of items such as grocery to online shopping, potentially with lasting effects. Grocers have no choice but to adapt their business models and delivery methods in real time to solve the online delivery problem, as early and late majority technology/innovation adopters are rapidly switching to online grocery delivery.
Alignment occurs when the interests of stakeholders in the supply chain are aligned such that their individual decision-making helps to optimize (and not diminish) the supply chain’s performance. An example of alignment is when a retailer who differentiates itself on quality works with its upstream suppliers to improve their processes and quality output (rather than, for example, applying pricing pressure which can cause suppliers to take cost-cutting measures and reduce quality). With COVID-19, we are seeing unprecedented collaboration amongst companies, levels of which are typically reserved for states of dire need such as times of war. Collaboration in supply chains is not something that comes easy or can be turned on like a switch. It takes time to build trust and working relationships with upstream suppliers. While the current crisis is pushing stakeholders in supply chains to work together (see, for example, medical device supply chains), the collaborations that will be most successful in reacting to the crisis are the ones where cooperative, working relationships already exist. This is because the means for information and knowledge sharing is already established, and the objectives between upstream and downstream in the supply chain are already aligned.
There have been, and will continue to be, many hard lessons learned in the world of supply chain from COVID-19. One of those lessons, that Agility, Adaptability, and Alignment win the day, we’ve known for a while. Unfortunately, for some, it took a crisis to remind us about it.
- Categories:
- Series: