Smart Utility Meters Drive Down Manufacturing Costs – If Managers Use Them
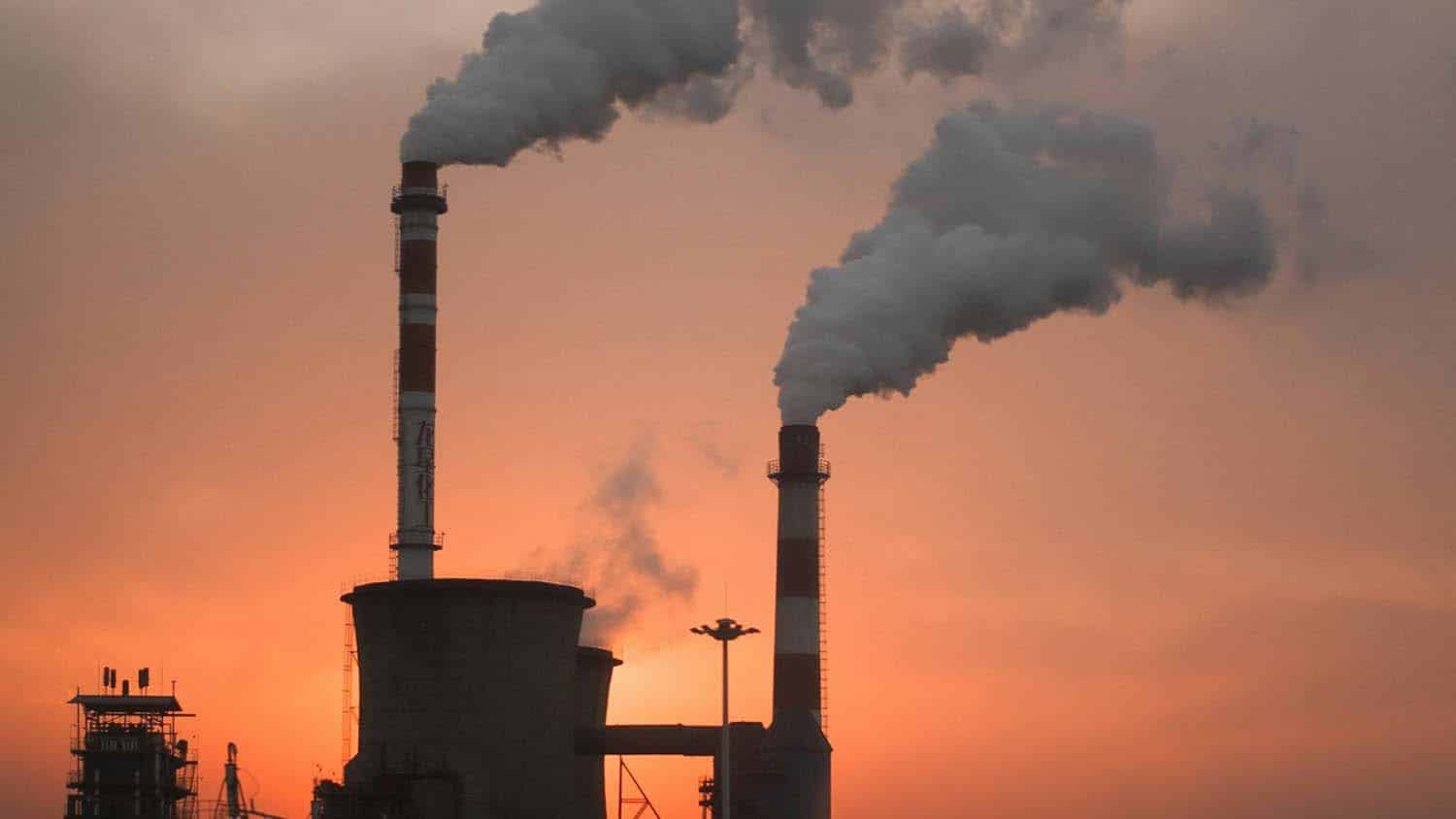
For Immediate Release
A new study of the extent to which “smart utility meters” can improve energy efficiency in manufacturing finds that the willingness of managers to actually make use of the technology is a key driver in reducing energy consumption and related costs. The work also serves as a proof-of-concept for using “event system theory” – which has historically been used to understand the impact of unexpected phenomena – to tease out the practical effects of planned actions in the business community, such as adopting new technologies.
“We had two goals with this study,” says Patrick Flynn, corresponding author of a paper on the work and an assistant professor of human resources in North Carolina State University’s Poole College of Management.
“First, we wanted to see how effective smart utility meters are at reducing energy consumption in the manufacturing sector, and which factors of the implementation approach might play a role there,” Flynn says. Smart utility meters give real-time data about power consumption to manufacturing managers, which they can use to make informed decisions about how to operate more sustainably.
“Second, there’s a lot of work out there that makes use of something called event system theory, which is largely used to help us understand the ripple effects of unexpected events such as the COVID pandemic or a stock market crash,” Flynn says. “But we know there are a lot of proactive events in the business community where companies make changes intentionally. We wanted to see if we could adapt event system theory to help us more fully understand the knock-on effects of these proactive events.”
To address both of these questions, the researchers looked at data from 87 plants, all of which were owned by a Fortune 500 company that adopted an energy management system which made use of smart utility meters. The researchers collected data on power consumption for each factory in the year before the smart utility meters were installed and for the year after the smart meter installation was finalized. The researchers also had data on when the smart meter installation took place, how long it took for the installation to be finalized, and how often factory managers accessed data from the smart utility meters.
“The first finding here is that, broadly speaking, the smart utility meters were a success,” says study co-author Amrou Awaysheh, OneAmerica Foundation Endowed Chair and associate professor of operations and supply chain management at Indiana University’s Kelley School of Business. “On average, energy consumption dropped by 7.46% across all of the factories. And the company saved more than $41 million per year in energy costs.”
However, the study showed there was significant variability from factory to factory, and that there were three variables associated with those differences.
“The strongest effect associated with greater energy savings was the extent to which managers accessed the smart meter data,” Awaysheh says. “In other words, our study suggests that people who actually used the data were able to achieve greater reductions in energy consumption. This is extremely important for managers.
“It isn’t enough to just invest in a new system,” Awaysheh says. “Managers need to make sure that system is being accessed and that behaviors are being changed as a result of the new insights.”
“The two other effects were less obvious,” Flynn says. “Factories that received the smart meters earlier also saw greater energy reductions. In addition, we found that the longer the installation process took, the more likely the factory was to have increased energy efficiency. And there was tremendous variation here, with some installations taking place in one month, while others took more than a year. Our hypothesis is that factories that experienced longer installation times were more likely to feel a greater sense of ownership of the smart meters and their potential.”
“Our work also helps demonstrate the viability of these types of investments for sustainability,” says Awaysheh. “The Department of Energy and policymakers around the globe want to increase investments in these kinds of systems to help reach net zero goals. Thus, when companies see that there is a financial benefit to investments in these types of systems, they are more likely to do so.”
The study also lays the groundwork for business researchers to go one step further.
“This work lays out a blueprint for how we can use event system theory to improve our understanding of any intentional change that a business makes, whether that’s installing a smart utility meter or adopting new human resources software,” Flynn says.
“Not only can event system theory help us understand the impacts that a proactive change had, it can also help us understand the impacts that a proactive change will have,” Flynn says. “And that means our research has greater potential for developing approaches that can help businesses thrive.”
The paper, “From Intent to Impact: A Proactive Event Approach for Amplifying Sustainability Across Time,” is published in the Journal of Management. The paper was co-authored by Amrou Awaysheh of Indiana University; Paul Bliese of the University of South Carolina; and Barbara Flynn of Fundação Getulio Vargas.
-shipman-
Note to Editors: The study abstract follows.
“From Intent to Impact: A Proactive Event Approach for Amplifying Sustainability Across Time”
Authors: Patrick J. Flynn, North Carolina State University; Amrou Awaysheh, Indiana University; Paul D. Bliese, University of South Carolina; and Barbara B. Flynn, Fundação Getulio Vargas
Published: March 22, Journal of Management
DOI: 10.1177/0149206323122437
Abstract: We extend event system theory (EST) to conceptualize proactive events and examine how event duration, timing, criticality, and disruption are related to two phases of change associated with an organizationally initiated event. Specifically, we explore the impact of a new sustainability monitoring system on energy consumption using longitudinal archival data from 87 manufacturing units of a Fortune 200 multinational firm. We use a variant of mixed-effects discontinuous growth modeling (DGM) to test EST propositions related to initial and longer-term changes associated with implementing the monitoring system. Results indicate that while the new sustainability monitoring system is effective in reducing within-unit energy consumption on average, there are significant differences in change magnitude between units. The magnitude of change during the pre-post phase was related to between-unit differences in event duration, timing, criticality, and disruption. Longer-term change patterns were related to between-unit differences in managerial criticality behaviors. The results empirically validate several of EST’s core propositions and provide an illustration of how DGM can be modified to study events that vary in onset and duration across entities.
This post was originally published in NC State News.
- Categories: