What’s Next for Unionization in the South?
Poole economics professor Steven Allen breaks down the unionization of a Volkswagen plant in Tennessee and looks ahead to a BMW vote later this month.
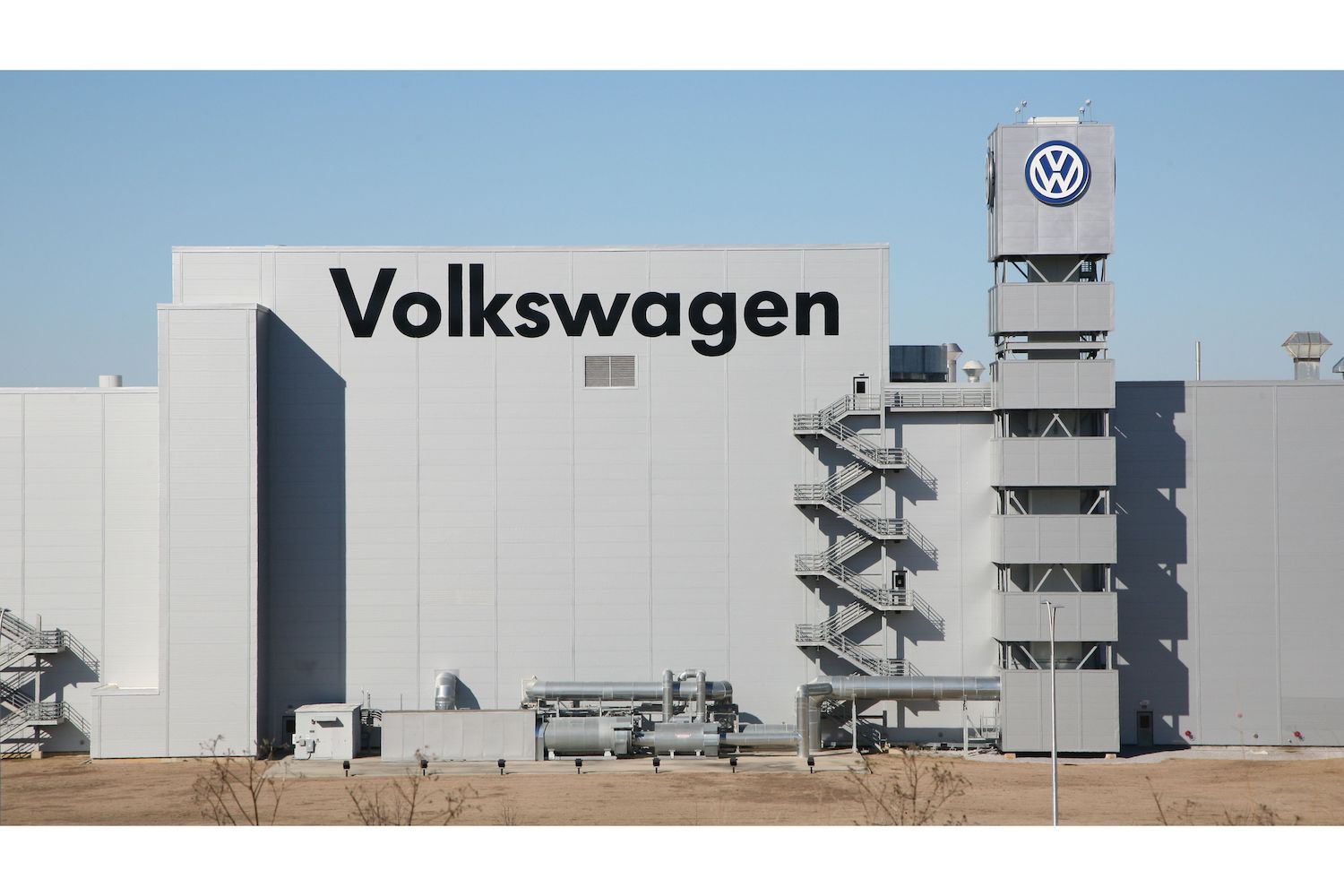
For decades, foreign-owned auto companies such as BMW, Mercedes, and Toyota have built and operated manufacturing facilities in the South. Southern states are appealing to these European, Japanese, and Korean automakers because of lower wages and near-zero odds of unionization.
But those odds may be changing. Last month, employees at the Volkswagen manufacturing plant in Chattanooga, Tenn., voted overwhelmingly to join the United Auto Workers (UAW).
Steven Allen, a professor of economics at the Poole College of Management, has studied labor economics for more than four decades. We caught up with him for insights into what this union victory means for similar future efforts in the South.
The UAW lost votes at this plant in 2014 and 2019. Why was it successful this time?
I believe there were two key factors. First, the UAW has new leadership that has been much more creative and energetic in its organizing efforts.
Second, that new leadership was able to obtain a lucrative contract with the traditional big three American automakers in Michigan last fall. Members are going to receive wage increases of at least 33 percent over the four years of the contract, with larger increases for those in the lowest pay brackets. That put wages for autoworkers in Michigan well above those paid in Tennessee, making union membership look much more attractive.
What will happen next at the Chattanooga plant?
This election was about whether the UAW would have the right to negotiate a collective bargaining agreement on behalf of Volkswagen workers. It remains to be seen whether the UAW and Volkswagen will quickly come to an agreement.
The union has two reasons to temper its wage demands. First, some portion of any wage increase will be passed on to consumers. Right now the price of an Atlas, one of the two vehicles made at the Chattanooga plant, is comparable to that of a Honda Pilot or a Toyota Highlander. Too big of a wage increase will tip the competitive balance, and Atlas sales are still below pre-pandemic levels.
Second, the Chattanooga plant has to be profitable. Volkswagen is a global company with production units on almost every continent. They have capacity to make the Atlas elsewhere.
Keep in mind that operating costs depend not just on wages, but also on productivity. Studies have shown that unionized operations partially offset higher wage costs with improved output per hour. Higher wages give management a more attractive applicant pool and the ability to insist on more output per hour.
Do you think workers at other auto plants in the South will unionize soon?
The UAW sure hopes so. There will be another vote at the Mercedes-Benz plant in Alabama starting May 13. Mercedes appears to be running a stronger anti-union campaign than Volkswagen did, and that could make a difference. The UAW says a clear majority of Mercedes workers have signed cards requesting union membership, but it remains to be seen whether cards will turn into votes. If the UAW somehow manages to unionize Mercedes, I expect the other nonunion, foreign-owned auto plants to follow suit.
There aren’t any big auto plants in North Carolina. Will the UAW victory in Tennessee have any impact on union organizing here?
Only 3 percent of North Carolina workers belong to unions, the second lowest percentage in the country. South Carolina is slightly lower.
Unions allocate scarce organizing resources to workplaces where they feel they have the greatest odds of success. In the face of our right-to-work laws and strong employer opposition, I doubt we’ll see too many organizing efforts focused on production and service workers. I’m equally skeptical that well-paid professional workers in some of the state’s largest industries such as biopharma, financial services, and information technology will be calling union hotlines.
However, history shows that union organizing success tends to take place in waves. In the US, there have been two historic waves: one for production workers in the 1930s and 1940s, and one for public employees in the 1960s. No one saw these coming. Unions have had some recent success in other states organizing graduate students, healthcare workers, and employees at Amazon and Starbucks. Surveys show that Generation Z and millennials are much more open to union membership than previous generations. Their union story has yet to be written.
- Categories: